Project 1050: Data Entry
Context
A client in the food production industry lacked visibility and control over daily food waste and overproduction. Each facility operated independently without a standardized process for tracking inventory usage, waste, or leftovers. This lack of data led to significant inefficiencies and financial losses.
What we automate
We developed a lightweight MVP for each facility to streamline daily data collection. The system enables staff to:
Record incoming product units
Track daily usage per product line
Log daily waste and leftover quantities
All data is automatically consolidated, cleaned, and visualized to allow managers to monitor operations in real time and make data-driven decisions without relying on manual spreadsheets.
Tools and Stack
To deliver a fast and cost-effective MVP, we used the following stack:
Google Sheets + Google Apps Script: Backend logic, data structure, and automation flows
Google Workspace Environment: Cloud integration and user access management
Android Tablets: On-site data entry at each facility
Power BI and Google Looker: Visualization dashboards to track usage, waste, and forecast needs
Impact
The system enabled the client to identify excess production and waste levels across facilities. Within weeks, they uncovered:
Over 50% excess production in specific product lines
Thousands in annual losses previously undetected
A clear roadmap to optimize purchasing, inventory, and production schedules
This MVP laid the foundation for a scalable digital solution across all facilities.
Diagram
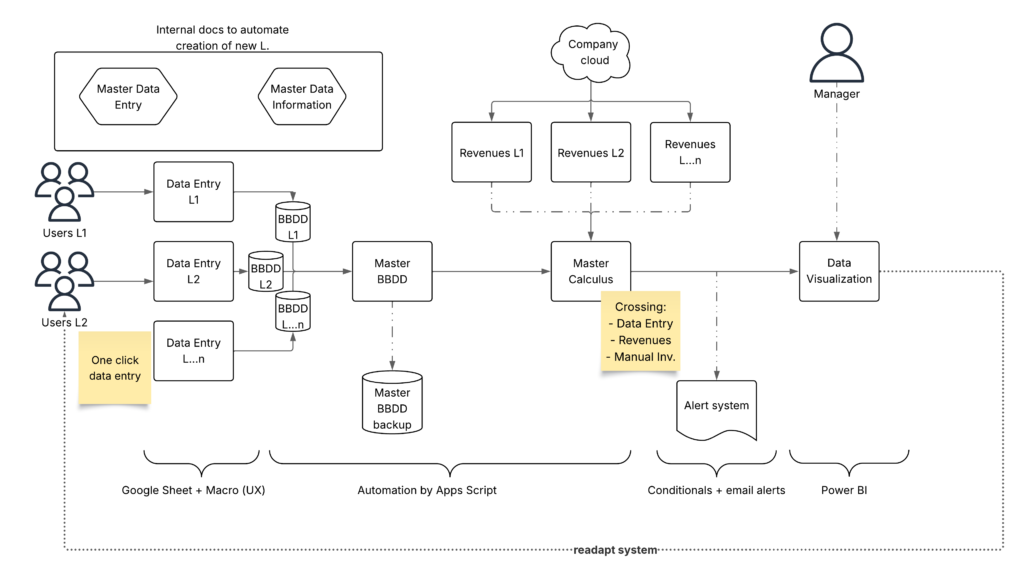
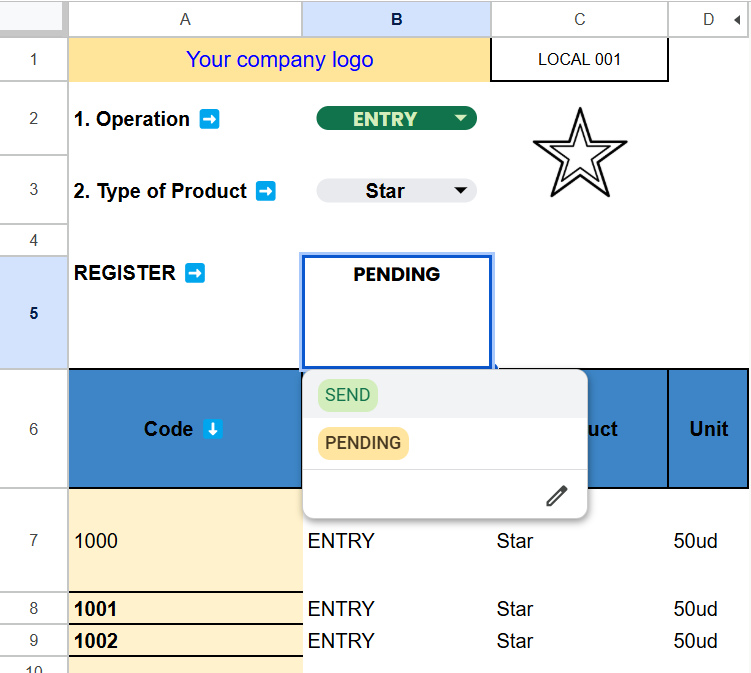
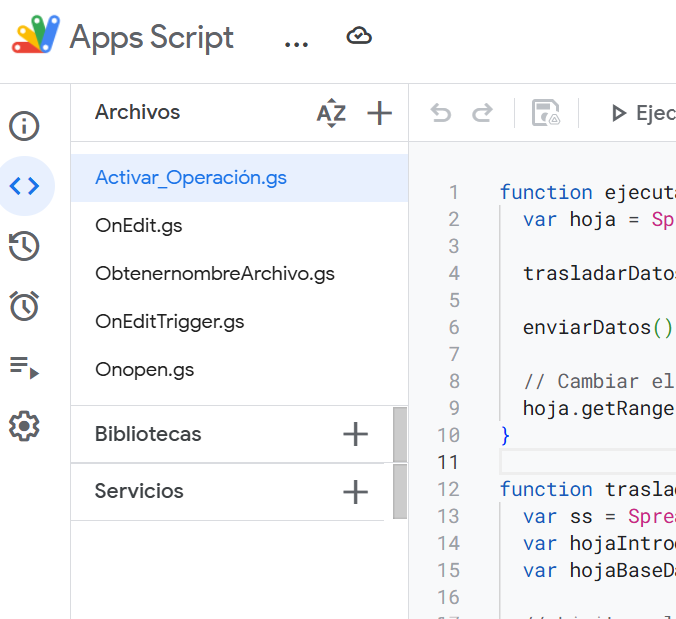
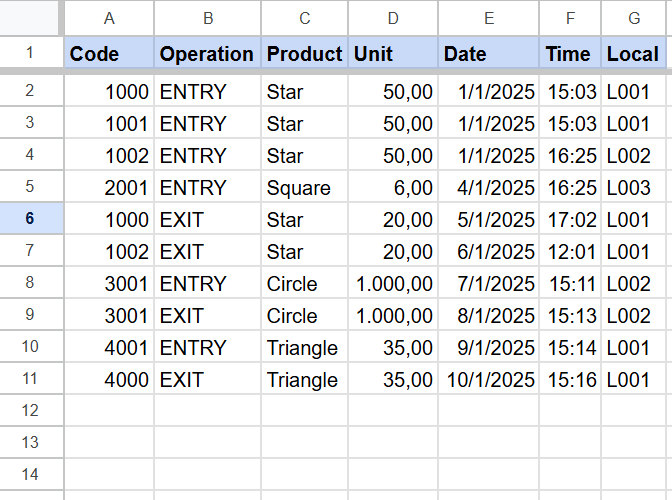
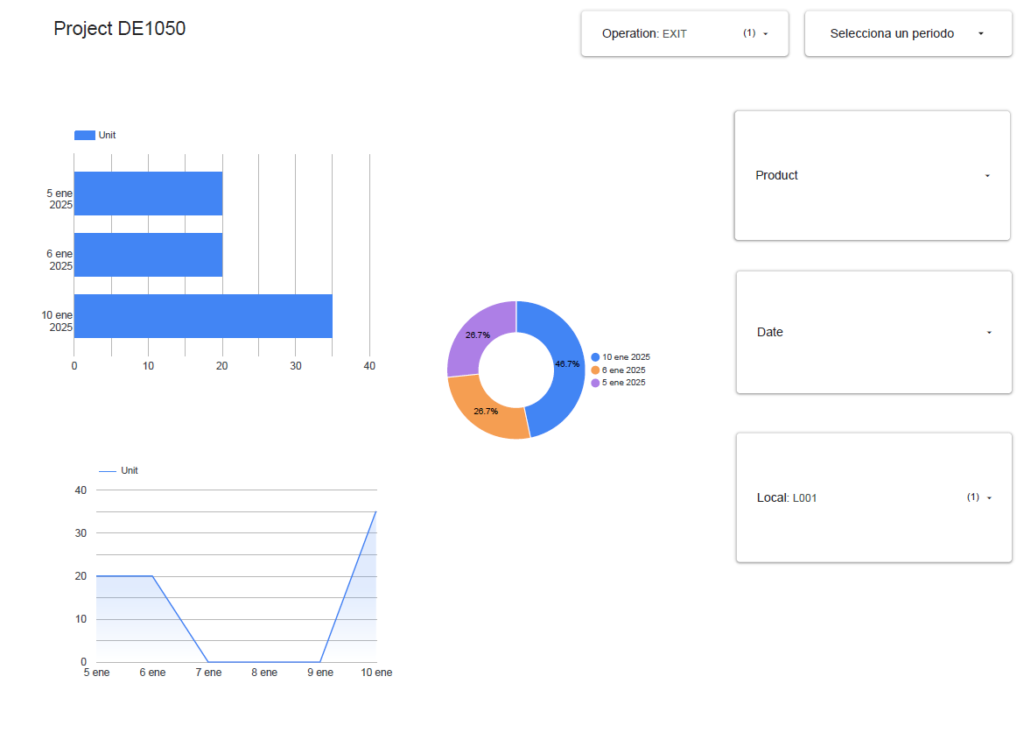
This project is a simplified representation and does not include confidential or official client data. The automation implemented aims to reduce human error by minimizing manual interaction in key stages such as data input, file processing, and reporting. The only identified risks in the process remain in manual data entry and the subjective interpretation of results.